Industrial Spray Booth
More than 30 years of experience in body & paint.
SIDE EXTRACTION (no civil work needed)
Double aspiration pit covered by galvanized reinforced grids, with structure support in both directions. With a capacity of 1.200 kg per wheel impact 200 x 200 mm
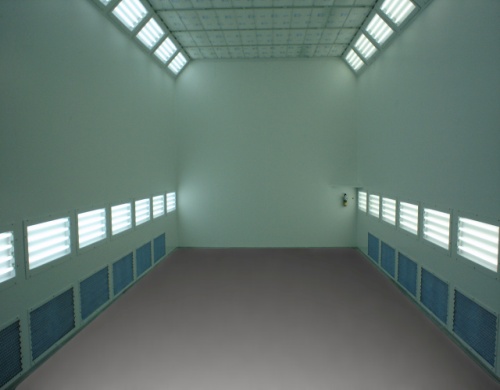
LATERAL WALLS
- Double face panels, pre lacquered, pressed and nerved, reinforced by metallic internal structure.
- With high performance thermic isolation (145 Kg/m³).
- Panels’ thickness: 50 mm.
- Four service doors placed in the lateral walls with safety mechanism automatic closing system.
PANELS ISOLATION
- Resin treated rock wool.
- Thermal conduction in mid temp. of 20º C
- Fire behavior: Not combustible
- Description: Panel with rock wool isolation
- Specific heat: 0,2 Kcal/Kg ºC
- Acoustic absorption: acoustic absorption coefficient (NCR) by 40 mm thickness
- 0,75 (Without intercalation)
- 0,85 (With intercalation)
- Elastic manufactured, easily to manipulate, not hygroscopic, odourless, it doesn’t putrefy. Without chemical reactions, humidity proof
ACCESS FRONTALS
- Frontals composed by a tubular structure with support function.
- With four leaf doors with tempered windows. Free vehicle pass maximum of W 3.900 x H 4.900 mm.
CEILING ENCLOSURE
- Galvanized plate trays that compose the enclosure of the ceiling and distribute air inside of the plenum
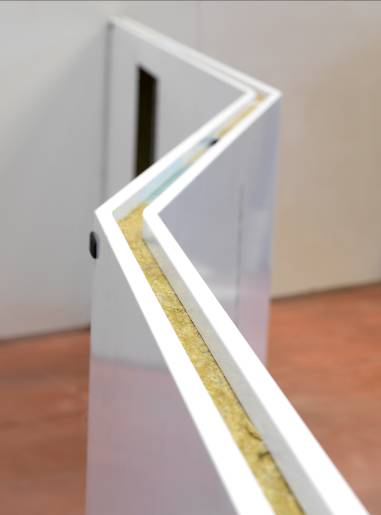
FILTER PLENUM (CEILING FILTERS)
- Divided in 14 + 14 modules of 2.100 x 1.100 mm., getting a filter area of ~65m²
- They are placed as filter sheets supported and fixed by an outline and grid that is fixed to the plenum structure by hinges.
- The filter blocking system (bolts and “L” washers) guarantees perfect air tightness, leaving no possibility of non-filtered air leaks.
- Filter material – Technical characteristics:
- Model: PA 560 G10
- Filters: Synthetic fibre
- Weight: 560 g/cm²
- Operating temperature: +100ºC with tip of +120ºC
- Fire behaviour: Class F5
- Rate of flow: 0,7 m/s (2.520 m³/h/m²)
- Efficacy: 97% (gravimetric)
- Final accumulated: 230 g/m²
- Leak in original load: 6 mm. H2O
Leak in final load: 40 mm. H2O
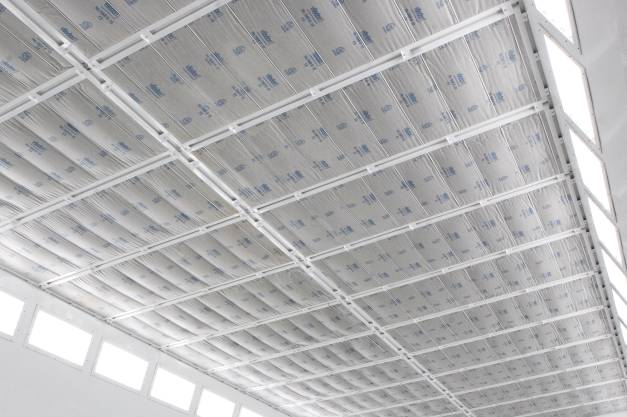
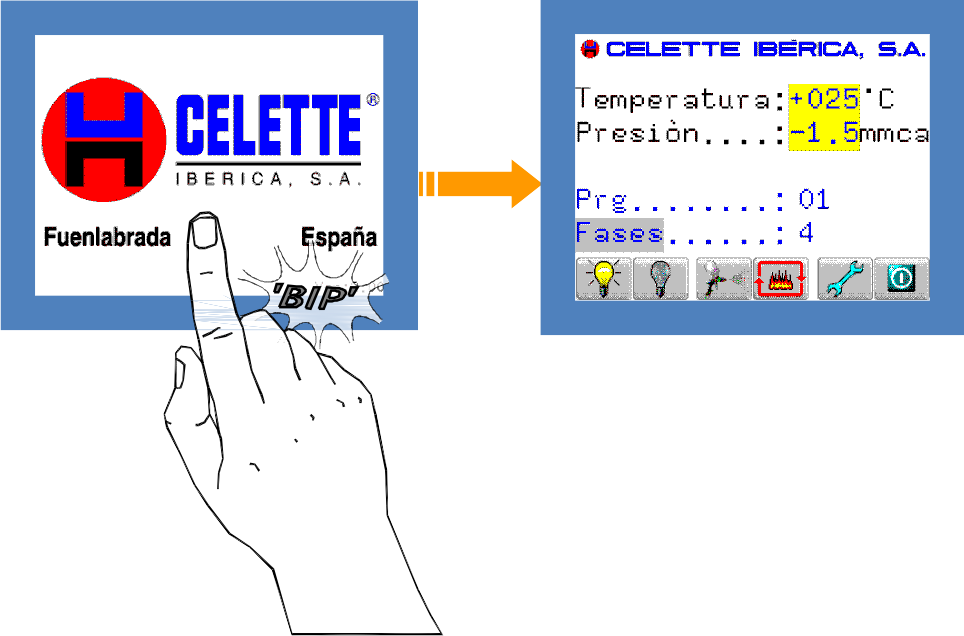
TOUCH SCREEN CONTROL PANEL
- Each parameter of the spray booth is commanded in the control panel by a PLC and a touch screen that can be easily programmed with the possibility to set 10 different work programs that can be used for any type of paint and piece or material
ILUMINATION
- One screen will be installed in the top and the bottom of each lateral panel, except in the panel with the service door, wich only will have the top screen.
- 4 fluorescent bulbs (30 W each) per screen. Total of 360 W
- The 19º angle for the installation of lighting was determined to guarantee a luminous level over 1.200 LUX with a correct air flow.
- Fluorescent bulbs powered by electronic reactance (not by ignitor)
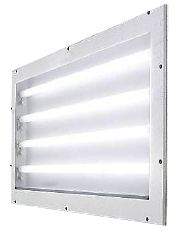
MOTOR GROUP Elements
A. Clean Air inlet to the motor group
B. Air outlet
C. Communication basement with motor group EXP 11
1. |
Recirculation valve that re-circulates 80% of the air in the drying phase, automatically commanded from the electric panel, allowing a fast temperature increase in drying phase. |
2. |
Pre-filter camera, with metallic filters easy to clean (no substitution required), and automatic controller (pressure sensor) for air gate and pre-filter saturation. |
3. |
Ventilation camera with a pressure drop max of 75 mm. H2O. |
4. |
Heat unit: AISI 304 stainless steel heat exchanger, with aerodynamic shape and heating pipes with horizontal smoke displacement and natural draught. With 210.000 Kcal/h thermal power and a Standard Combustion gas burner. |
5. |
Electric cabinet that controls the motor group with a touch screen control panel. With all the safety elements needed to the correct work of the generator and other important elements like terminals, differentials, electro thermals, relays, power transformer, starter, frequency shifter and others electrical components. |
6. |
Extraction camera built with the same shape and capacity as the ventilation group. On the group a frequency shifter acts in the speed of the motor keeping constant pressure by INVERTER technology, and reducing remarkably the electrical consumption. INVERTER is commanded by a differential pressure sensor. |
7. |
Automatic controller (pressure sensor) for air gate and pre-filter saturation. |
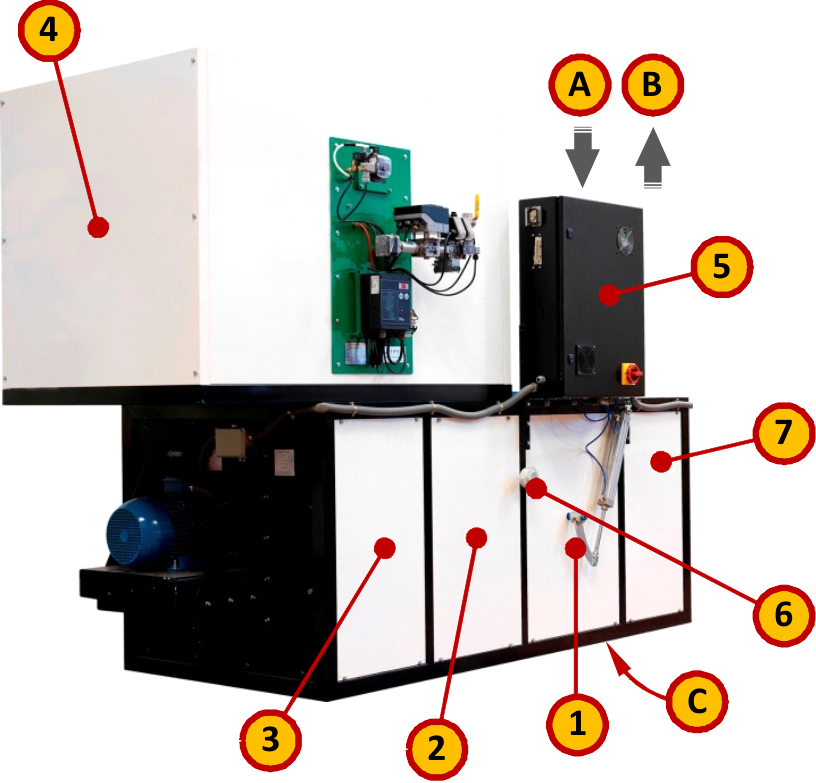
Reaction Turbines | Yes |
Quantity of Motors | Each group - 1 Total booth - 2 |
Impulsion Motor Power | Each group: 11 Kw. (15 C.V.) Total booth: 22 Kw (30 C.V.) |
Burner | Gas Standard combustion burner |
Burner power | Each group: 210.000 Kcal/h. Total booth: 420.000 Kcal/h. |
Pre-filters | Metallic (easy maintenance) |
Please feel free to fill out our enquiry form below with any questions or queries you may have regarding our services. We will respond as quickly as possible.